
Custom Case Design
Our Pelican engineers and partners will help you design the exact case you need for your equipment. Whether you provide CAD files or the physical sample, we can determine what you need for ultimate protection.
Case Foam - Four Ways to Design
Our customers are as diverse as their case applications- sophisticated engineers, government agencies and tech startups, to name just a few. That’s why we’ve developed a flexible approach to planning your foam design, even if it’s a “back of the envelope” sketch. Below are some of the ways we can get your project started:

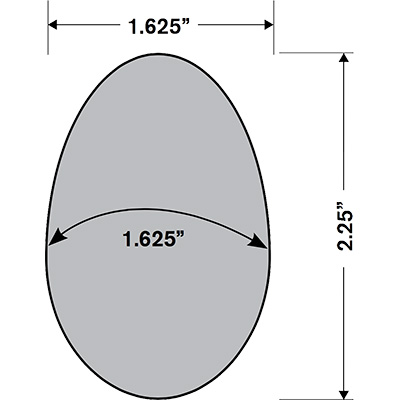
Provide Pocket Dimensions
Customer supplies diagram with foam pocket dimensions.
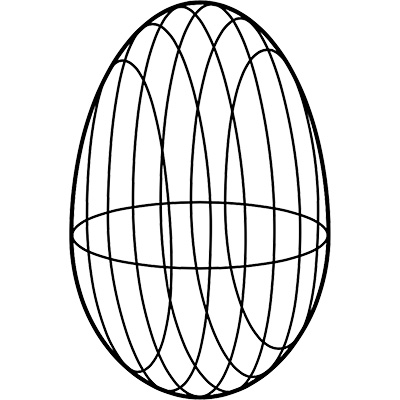
Send Part CAD File
Customer provides equipment CAD file.
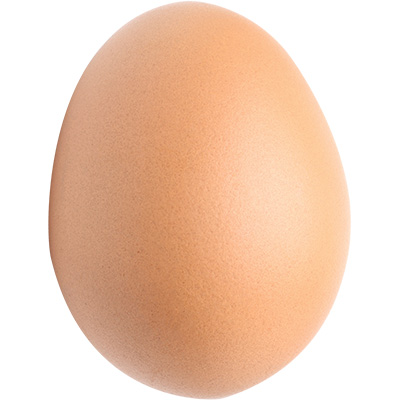
Send Physical Sample
Customer sends physical equipment or part.
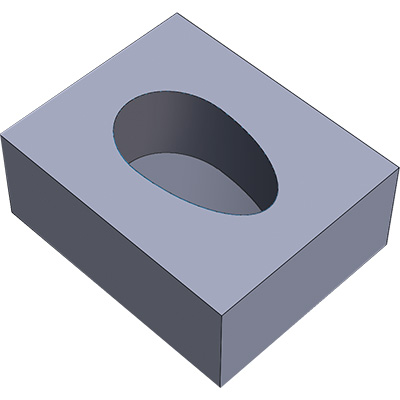
Customer Provided Foam
Customer produces 3D foam CAD and uploads to Pelican .

Custom Testing
For customers that need to certify a case will perform to specific requirements, product testing can be ordered. A battery of rigorous tests are available (see below) to replicate or exceed adverse conditions in the field.
Drop Test
- Six foot cube reaction mass of reinforced concrete. A hoist capable of lifting 1 ton, and a quick release mechanism with a load capacity of 1⁄2 ton.
Impact Test
- Falling dart – 84” drop height with darts weighing between 5 and 15 lbs.
- Penetration test for category 1 containers - ATA 300 paragraph B-2-5.
Thermal Test
- Walk in environmental chamber 6-foot wide by 8 foot high and 8 feet deep with a thermal range of -100°F to 200°F.
Immersion Test
- Internal dimension of the chamber is 54” x 30 x 36”H. Able to simulate immersions up to 2 meters.
- Small immersion tank capable of immersions up to 1 meter on small IM cases.
- 80-inch deep large immersion tank
Rain Test
- Small rain chamber capable of up to 4 inches per hour.
Pneumatic Pressure Test
- Digital manometer – 10 psi max.
Vibration Test
- L.A.B. servo hydraulic vibration system; 0 – 300 Hz.
- Sinusoidal with pre programmed profiles for STA Integrity test procedures 11800, 14200, 1A, 1B, 1E, 1C, 1D, 2A AND 2B, 3–50Hzsweepwith1G constant input, 1-inch dwell for loose cargo bounce, Mil-Std-648C; 5.3.2.
- Random Vibration with pre-programmed profiles for ASTM D 4169 Air/Truck/Rail levels 1, 2, and 3, and ISTA Integrity Test Procedures 1E, 1H, 1C, 1D, 1F, 3C, 3D, and 3E.
Mitutoyo Hardness Test
- Metal evaluation of product used in cases.
Compression and Tensile Test
- Instron compression tester.
- Load range of 6600 lbs on small items.
Leak Test
- Rain: Small rain chamber capable of up to 4 in. per hour.
- Digital manometer - 10 psi max.
Injection Molded Cases
Product testing on randomly selected production samples of injection molded cases are performed as follows:
- Drop Test - Varies by model number. 1510/im2500 tested to multiple 6’ drops, larger cases tested to 3’ drops.
- Falling Dart Test - 28.4lb dart with 1” bullnose tip (all cases). Minimum 3’ drop height up to 8’ drop height on certain models.
- Mobility Test - Models with wheels/trolleys towed with weight load at 5mph for 1000 yards (load varies by model).
- Water Ingress - Most models are subject to a submersion test under 6” of water for 30 minutes. Otherwise a spray test of 3 minutes to each side is used.
Quality Control
We stand behind our products and guarantee their performance. With manufacturing credentials like ISO 2001:2008 certification, Peli has won numerous awards from the National Institute of Packaging, Handling and Logistics Engineering (NIPHLE).
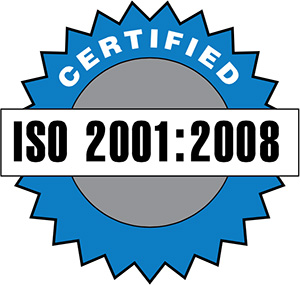
